1. DOE分析的定义
DOE是实验设计(Design of Experiments)的简称,它是一种统计工具,工程师可以用该工具查看某些干预(如更改实验工艺变量)对成型质量的影响。该工具还可以帮助您确定哪些工艺条件对于给定质量指示器的影响最大。要完成实验设计分析,DOE 生成器需要改变所选工艺条件并运行一系列实验,然后基于用户定义的质量指示器计算结果。这使得工程师可以更快捷的解决一系列跟充填,保压,冷却相关的问题。
2. DOE原理及分析流程
DOE分析是运用正交试验的原理,将成型过程中的一些参数当做变量输入,进行排列组合运算,这些变量可以是成型条件,如模温、料温、流动速度、成型压力、保压压力和时间,冷却温度等,也可以是产品壁厚等等,Moldflow会根据这些条件组合计算出对分析目标影响最大的因素,并从输出中给出推荐的范围。
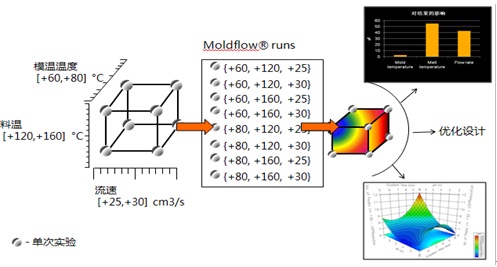
DOE分析步骤为:选择实验类型 > 选择或者输入变量 > 确定零件的质量标准 > 继续分析。选择或者输入变量:通过实验设计 (DOE) 分析可查看某些干预对零件质量的影响。输入变量即为干预。例如,您可以更改熔体温度或冷却液入口温度,调整保压压力、保压时间等参数,然后查看各个参数的更改对零件质量的影响。 质量标准:通过实验设计 (DOE) 可查看某些干预对零件质量的影响。质量标准即是定义零件质量的指示器,如缩痕深度、压力、零件质量或冷却时间、翘曲变形等等。
3. DOE分析优势及关键技术指标
传统的试错法实验需要花费较多的材料、人力成本、成型机的消耗等等,实验设计 (DOE)与更为传统的试错法实验相比,DOE 的优点是可从测试数据的生成阵列获得数量显著增多的高质量信息。通常,可在设计阶段随时运行 DOE 分析。但最好在选定材料和浇口位置并执行初始分析之后再运行 DOE 分析。 DOE分析适用于中性面、双层面和 3D 网格类型,该分析适用于所有成型过程。DOE分析有以下优势:
1) 更快、更好、更经济 2) 界面易用 3)以最小的实验次数获得更多的信息 4) 为每个优化目标提供最优解
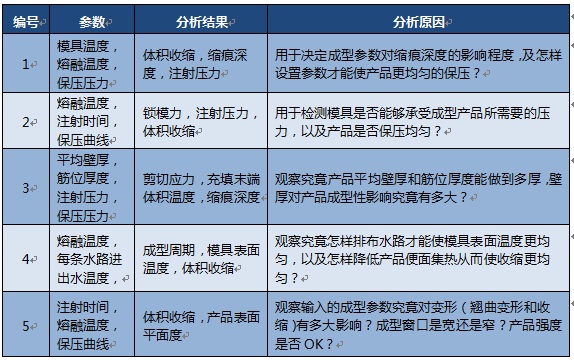
4. DOE分析速度提升小技巧
在做DOE分析时,尤其当设置变量较多时,会产生的很多的分析组合在排队等候,这样分析速度会很慢,如果电脑配置比较好,可以采用以下方法提升分析速度:
1) 打开分析管理器,在“Distribution queue max. running jobs”中增加选项中的最大运行数量;
2) 将分析任务分配给不同电脑运算
3) 采用云端运算(Moldflow新技术)
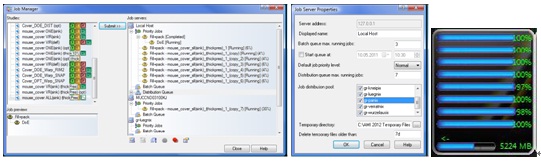
5. DOE运用实例
案例之一,用DOE分析优化缩痕
1)图为鼠标下盖档案,产品中间有3个Boss孔,考虑到Boss孔需要锁螺丝,要承受一定的力量,Boss孔肉厚设计较厚,这样在成型时对面会有缩痕风险.现在用DOE分析来计算出既不出现缩痕、又保证强度的最佳壁厚出来.
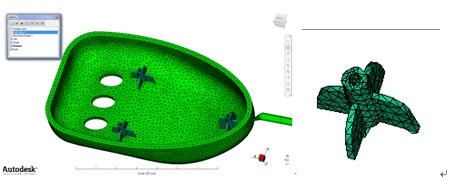
在设置参数时,我们将Boss孔及支撑肋的有限元单元单独定义成变量层,设置变化范围,同时要选择其他可能对缩痕有影响的其他因素当做变量输入,例如保压时间和压力等,填充时间,冷却时间温度,模温料温等,并设置变化范围。选择原则可以参考上面我们总结的DOE分析技术指标
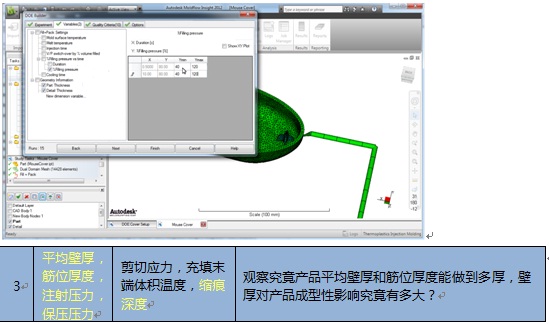
2)分析结果
典型的DOE分析结果是以3D响应图输出(当输入有多个变量时),如下图,两个横坐标表示分析出的对缩痕影响最大的两个因素,一为壁厚变化,另一个为保压压力,其中保压压力对缩痕的影响非常明显,而产品壁厚也有影响,但限于壁厚变化范围有限,所以显示出来的影响也有限。根据分析推荐的壁厚和保压条件,再次输入Moldflow进行运算。
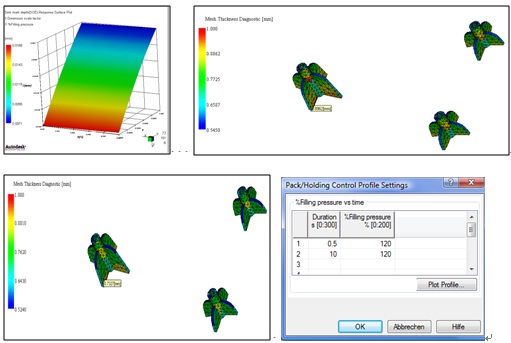
3)采用优化条件运算,作结果对比
通过对比缩痕值可以发现,原始条件下产品Boss孔对面会有可见缩痕,但输入优化后的条件(调整壁厚和保压压力)再次运算发现,缩痕明显减小,在可以接受范围内。
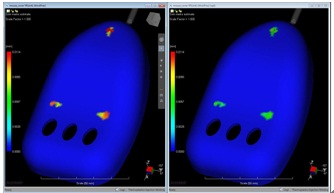
案例之二,用DOE分析优化变形
1)图示产品初步分析之后发现变形很大,之后将产品模型中变形最大的位置的节点找出来,再在产品底部设置基准锚点,将变形最大的节点和基准点之间距离定义为关键尺寸,通过控制关键尺寸的变化来达到控制变形的目的。
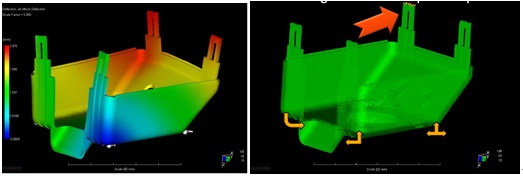
之后设置可能对变形有较大影响的参数作为变量,这里选取了模具温度,熔融温度,V/P切换位置,保压压力和时间,作为分析的变量(说明:当产品壁厚不允许更改的情况下,不能将壁厚作为变量输入,否则分析出的方案有效但不能被采用,同样是无效的)
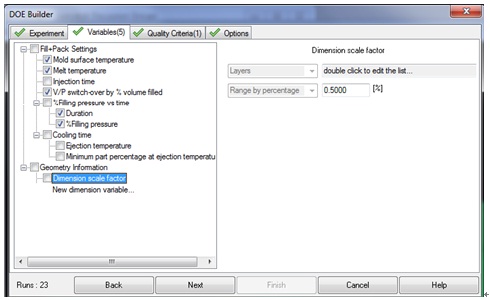
2)分析结果
从以下分析结果曲线可以看出,DOE分析找到的对变形影响最大因素是保压设置,包括保压时间和压力,根据分析推荐,重新设置保压曲线,进行分析 。

3)结果对比
下图左边是产品原始变形情况,变形非常明显,通过DOE分析优化参数之后,将优化参数输入分析模型进行重新分析,得到如右图所示变形结果,从变形数值可以看出变形量明显减小。
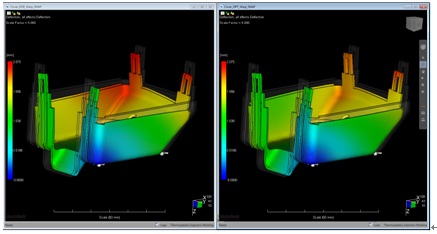
更有效的对比方式如下:将之前变形的产品和优化后的变形产品档案叠加起来,可以非常直观的看到产品变形有明显改善。
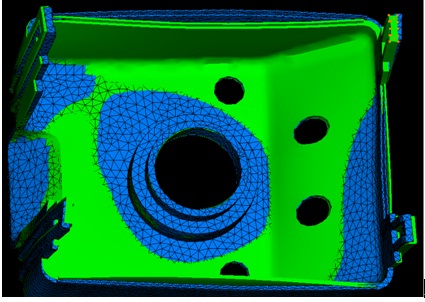