多型腔热流道注射模的浇注平衡分析
在一模多腔的注塑成型中,保持塑料熔体在浇注系统中的流动平衡性十分重要。这直接影响到各型腔的填充时间、注射和保压压力,以至体积收缩率的均衡性,进而影响产品的质量。然而,对于冷流道模具的热流道改造,由于模具的模板尺寸、型腔布置和浇口位置都已经固定,要实现自然的平衡流道系统设计已不可行。因此,流道设计仍考虑为非平衡式流道布置,但这又势必会影响产品的质量。
如何在这种流道系统的设计中实现平衡浇注对于模具制造商而言非常关键。近年来,许多模具制造商开始应用热流道技术,并在模具设计中预先使用Moldflow软件进行模拟分析,极大地提高了模具设计的效率和准确性。
本文以克朗宁公司改造一具拥有18模腔的瓶盖热流道注射模为例,深入分析了Moldflow软件在优化流道设计,尤其是改善浇注平衡方面的应用。针对该注射模从主流道到各型腔的流道长度均不相等的特点,克朗宁公司通过利用Moldflow软件优化流程中各段流道的直径,使塑料熔体从主流道进入各型腔的压力降保持相等,从而保证了熔体能够同一时间充满各型腔,实现了各个型腔制品的平衡浇注成型。
一、流道直径的初步设计
首先,根据各浇口位置和型腔的布局,确定了如图1所示的流道分布。然后,根据物料的特性、单个型腔的注射量和浇口位置等参数,确定相应的热流道分喷嘴的流道直径为6mm,并由此确定第二层分流道的直径也为6mm。
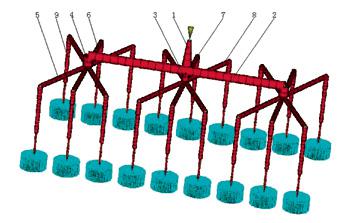
图1 热流道浇注系统的布置情况(其中,1-主流道喷嘴;2-第一层分流道;3-两层分流道间的中央连接流道;4-两层分流道间的两侧连接流道;5,6-第二层两侧分流道;7,8-第二层中间分流道;9-顶针式喷嘴和浇口)
一般,在热流道模具中,熔体与流道壁面的热交换和流道截面所产生的摩擦热非常少,因此熔体因温度变化而导致的黏度变化相比冷流道系统也较小。因此,在流动分析中,按熔体在各流道中剪切应力不变的理论,可以得到各级流道直径的计算式(如下述方程所示):
式中,N——流道的分叉数;di——上游流道的直径,mm;di+1——下游流道的直径,mm。
根据流道的分支情况和分喷嘴流道的直径,可计算出第一层分流道的直径为10.9mm。考虑到实际加工和流道中熔体传输的压力损失,可适当增大这一分流道的直径,这里初步确定为12mm。由于两层间连接流道与主流道喷嘴之间的距离较近,流程较短,这时熔体的压力损失相对较小,因此可适当减小连接流道的尺寸,初步确定为8mm。其他各段流道的直径可参见表1。
二、Moldflow初步填充分析
完成初步设计及三维造型后,可利用Moldflow软件对流道进行填充分析。本次试验所采用的原料为HDPE,各工艺参数设定为:料温为220℃,模具温度为40℃,保压压力为注射压力的80%。
1、填充时间分析
如图2所示,由于主流道喷嘴至各型腔的流程长度不同,因此各型腔的填充时间亦不相同。经测算,流程最长的型腔完成填充需要0.2518s,而最短的流程仅为0.2081s,流动的不平衡性达到了17.3%。这势必会导致各型腔的压力分布不均,进而影响制品的质量。
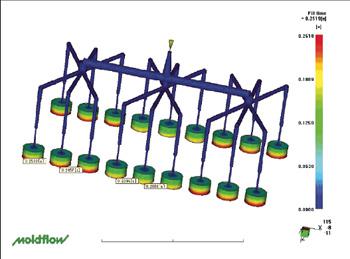
图2 非平衡流道布置的注射填充时间
注射0.2081s后,流程最短的中央型腔填充完全,此时对应图3上主流道位置的输入压力为55.87MPa。在此之后,压力曲线急剧上升,在注射填充结束时达到最高压力66.88MPa,说明各型腔的熔体填充流动过程很不一致。
2、V/P转换点压力分析
如图3所示,处于模板中央位置的型腔由于过早地被充满,在填充结束时,分喷嘴进料点的压力为57.64MPa,该型腔内的压力也高达42.15MPa。与此同时,处于模板两侧的分喷嘴进料点的压力为47.94MPa,型腔内压力接近0。这将会造成中央型腔形成过度保压,而两侧型腔的保压不足,从而导致中央型腔所成型的瓶盖冷却固化的收缩率较小,模具分型面的中央有可能出现溢边,而模具两侧的型腔所成型的制品因压力不足而收缩率过大。
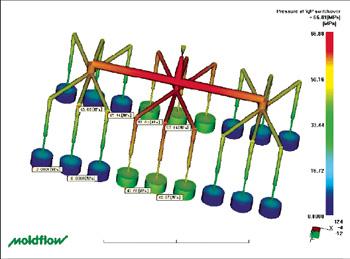
图3 非平衡流道布置的V/P转换点压力分布
三、Moldflow流动平衡分析
通过上述分析可知,原始的热流道系统设计并不合理,因此必须对其进行流道改造。在本实验中,通过应用Moldflow软件对具有非平衡流道布置的流道系统进行改进,很好地实现了平衡浇注,从而得到18个具有良好一致性的成型制品。
改造的关键是对流道尺寸的约束条件进行设定。由于热流道的分喷嘴与注射量直接相关,并且有对应的系列规格,因此设定分喷嘴的内径为6mm,同时将第二层分流道7和8的直径设置为固定值,为6mm。对于第二层两侧的流道5和流道6,将其直径设置为允许有6~10mm的约束变化,而其余各段流道的直径设置为无约束。然后,根据已有的填充分析压力曲线,将目标压力设定为60MPa,其他注塑工艺参数不变。经Moldflow自动分析运行,流变学平衡的各段流道的直径优化结果见表1。
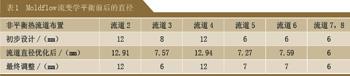
1、填充时间分析
浇注平衡后的填充分析结果如图4所示。经过对流道直径进行优化设计,各型腔的填充时间基本趋于一致,最长流程的填充时间为0.2514s,最短的为0.2392s,流动不平衡性从原来的17.3%降低至4.8%。
图4 流道直径优化后的注射填充时间
2、V/P转换点压力分析
图5为流道直径经优化后的V/P转换点分布情况。由图可知,主流道位置的压力为56.8MPa,这与预先设定的60MPa的目标压力非常接近。同时,经过浇注平衡后,整条主流道位置的压力曲线变得非常均匀平滑,没有压力陡增的情况。
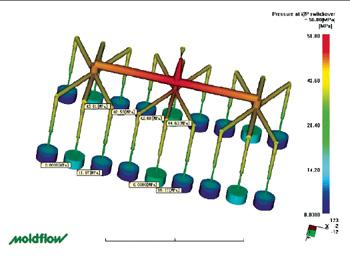
图5 流道直径优化后的V/P转换点压力分布
与图3相比,各分喷嘴进料点的压力集中在42.53~44.63 MPa之间,各型腔内的压力分布的均匀性也得到了很大的改善。这说明,流道直径经过优化后,熔体流动基本平衡,而且各型腔的压力分布均匀,效果比较理想。
3、体积收缩率分析
为最终确定制品的成型情况,克朗宁公司将流道直径优化前后的模型进行了流动和保压分析。通过比较图6和图7可以看到,由于各型腔的压力差过大,最初的非平衡布置流道会导致各制品的体积收缩率出现较大的差异,而通过Moldflow优化后,各型腔在充模完全并保压一段时间后,由于各型腔的充满时间相近,因此各制品的收缩率基本一致(见表2)。

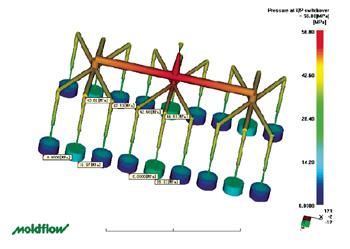
图6 非平衡浇注的各瓶盖的体积收缩率(保压压力为填充压力的80%,保压时间2s)
四、设计方案的最终调整
通过流道平衡分析后所得到的流道直径尺寸均为小数。由于在实际加工中,深孔钻的刀具直径都是标准系列,因此应该对流道直径做出适当调整(见表1末行)。
为了验证调整方案的可行性,需要在维持原来的注塑工艺参数不变的情况下,再次进行Moldflow填充分析。分析结果显示,最长和最短的充模时间分别为0.2496s和0.2358s,流动的不平衡性为5.5%。在整个填充过程中,V/P转换点在主流道位置的压力为57.9MPa,压力变化均匀。对比图4、5和7可知,调整方案的结果与通过Moldflow优化后的填充分析结果基本一致。
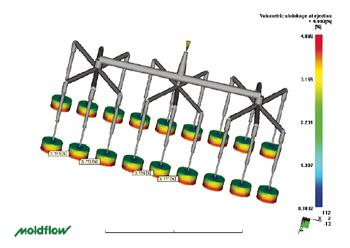
图7 平衡浇注制品的体积收缩率(保压压力为填充压力的80%,保压时间2s)
五、结论
在这一热流道的设计过程中,由于受到多型腔布置、浇口位置、模板尺寸和加工工艺等诸多因素的限制,各型腔的填充时间和压力尚未完全达到理想状态。经过应用Moldflow软件对流道设计进行分析和优化,可使非平衡流道布置的多型腔注射基本实现平衡浇注,从而保证多型腔注射制品的尺寸精度和质量的一致性。