如何运用Moldflow模拟薄壁注塑成型
目前关于薄壁注塑成型的定义,Mahishi和Maloney把其定义为流长厚度比L/T(L:Length,流动长度;T:Thickness,塑件厚度;L/T也简称为流长比)在100或者150以上的注塑为薄壁注塑; 一般薄壁往往精度要求很高,一般液压机未必能够达到这个精准度,所以需要更特殊及具有高速、高压性能的注塑机
Autodesk Moldflow仿真软件具有注塑成型仿真工具,能够帮助验证和优化塑料零件、注塑模具和注塑成型流程,可以用来分析薄壁塑件的填充行为,以及薄壁塑件注塑中工艺参数的选择; 但不能充分描述在薄壁注塑成型中所有的影响因素,实验结果与模拟结果之间几乎都存在差异,这可能是由于存在实验和计算误差,但更重要的原因可能是由于在模拟中,一些重要的物理、热学或其他性质的简化造成的,所以运用Moldlfow分析薄壁注塑成型时,需要考虑以下问题点并进行相应的修正。
一、压力对粘度的影响
研究中发现,在诸多影响模拟精度的因素中,粘度的压力依赖性排在前列,如不考虑压力对粘度的影响,随着压力的增加,模拟误差将增大(图1)。同时还发现,熔体的密度变化、由压缩功转化的粘性热甚至熔体的粘弹性本身都可能会影响薄壁注塑成型的模拟精度。
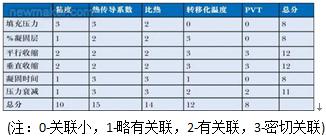
图1 压力对粘度的影响模拟结果 表1 材料属性与Moldflow分析结果(实际成型效果)的关联性
1.1 Moldlfow剪切粘度模型
聚合物为非牛顿假塑性流体,具有剪切变稀的特性,其粘度不仅受温度的影响,还受剪切速率的影响。Moldflow默认的粘度模型为Cross-WLF模型。这一模型能在较宽剪切速率范围内反应熔体流动规律,适应温度范围广,能更准确地描述伴有冷却效应的熔体流动。特别是当温度接近于玻璃化转移温度时,能很好拟合粘度的迅速增加。
式(1)为Cross-WLF粘度模型的运算式:
这也是经典的7参数模型(n, D1, D2, D3, A1, A2)其中n是非牛顿指数,1-n表示剪切变稀曲线的斜率;是剪切变稀行为开始的剪应力;D2对应低压下的玻璃化转移温度;D3是压力影响系数,表徵粘度对压力的依赖性,在高速高压成型分析中,比如薄壁成型,必须考虑粘度的压力依赖性。
表2 几种常见材料的D3值
1.2 Moldlfow拉压粘度效应
Cross-WLF模型考虑的是剪切粘度,不考虑拉压粘度。在浇口直径变化较剧烈的情况下往往会有较明显的拉压粘度效应,造成更大的压力损失,此时需要考虑Juncture loss的Bagley修正系数C1和C2(采用3D求解器考虑Extension viscosity模型系数A和B)。如Moldflow未提供修正系数,可在Moldflow帮助档中查找经验数据进行修正。如果分析时不考虑拉压粘度影响,分析获得的注塑压力会小于实际值(20%),锁模力可能会偏大。
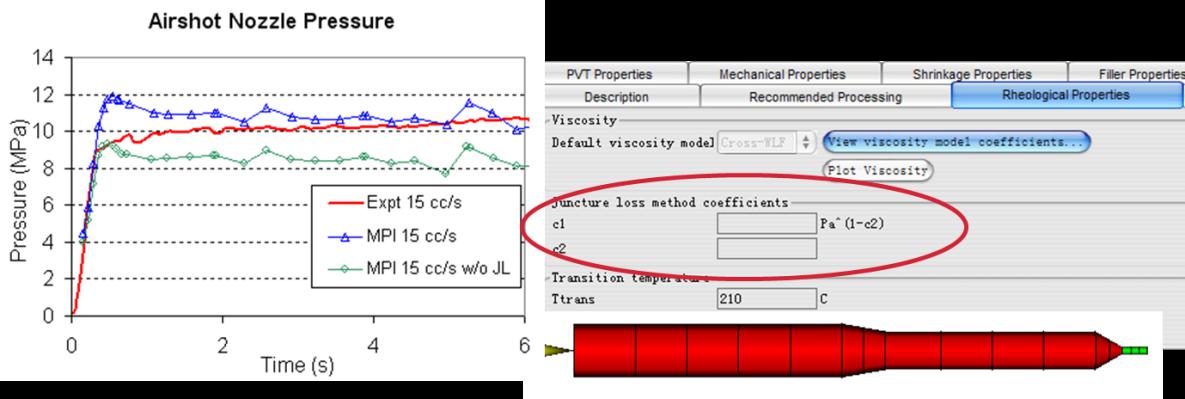
图2 接合点损失法系数:Juncture loss
该参数用于修正在Beam单元中以下位置的压力损失
1.直浇道和射嘴的位置以及浇口等截面急剧变化的位置
2.流道中截面变化的位置(H流道中主流道到分流道的位置)
二、Moldflow接触面传导系数修正
针对薄壁产品,HTC值(接触面传导系数)是传热要考虑的一项重要属性。研究表明,当塑件的厚度减小时,冷凝层对流动的影响将会以指数形式增加,这说明了冷凝层在薄壁注塑成型中的影响很大。Moldflow Plastic Insight 6.0之前默认的HTC是一恒定的值25,000。试验表明,实际的HTC值在填充、保压、冷却过程是变化的,并且远低于25,000,否则对于薄壁件分析时会出现高估短射的情况。Moldflow2014版本中的默认设置如下图 。
图3 接触面传导系数
经验公式中5000对应的是厚度为2.5mm;针对于薄壁成型,需要对接触面传导系数进行修正;厚度降低,接触面传导系数按线性比例降低;而且填充、保压、冷却过程中接触面传导系数是逐步降低的。
三、案例分析
掌上电脑后壳,见图4,厚度为1mm,材料为PC,采用高速高压成型,;实际注塑压力接近300MPa;
图4 产品模型
未进行修正前,分析出来压力为162MPa,锁模力为605T。与实际对比发现压力结果偏小,锁模力偏大;具体结果如图4.
图5 压力结果和锁模力结果
进行参数修正后,分析出来压力锁模力结果和实际接近;其中压力结果291MPa,锁模力结果473t.
四.总结
综上所述,利用Moldflow来模拟薄壁注塑或高速高压成型时,由于工艺的特殊性,很多注塑条件和常规注塑有了很大的不同;分析人员进行粘度依赖性修正,拉压粘度修正,以及接触面传导系数修正等后,还是可以准确预测产品的充填、压力以及锁模力,为模具设计时选择注塑机吨位提供参考。