Moldflow翘曲机理及计算模型
一、翘曲的理论和概念
导致翘曲的因素:导致翘曲的因素很简单,就是零件收缩过程中出现了变化。如果零件在所有方向和位置能均匀收缩,则零件只会变得越来越小,但不会发生翘曲。如果您可以控制这种收缩率变化,就可以控制翘曲。
零件的收缩率变化,收缩率变化可分为四个方面:
●区域之间的收缩率。
●塑料横截面厚度方向上的收缩率。
●平行和垂直于材料取向方向上的收缩率差异
●厚度方向上与平面内收缩率的收缩率差异
各四个方面收缩差异概念:
区域之间:
收缩率可视为接近浇口和接近填充末端的收缩率差异。也可视为零件较厚区域与较薄区域的收缩率差异。
厚度方向上 :
收缩率变化由塑料横截面一侧相对于另一侧的温度变化引起。总而言之,就是型腔和型芯之间的温度差异。
平行和垂直于材料的取向方向:
纤维或塑料分子的取向排列会导致平行和垂直于材料取向方向上出现收缩率差异。这与流动方向大致相同。通常对于未填充材料而言,平行于流动方向上的收缩率将更大。对于填充材料,流动方向上的收率往往会受阻,因此垂直于流动方向上的收缩率会更大。但是,纤维对收缩率的影响非常复杂,并且收缩行为可能会随零件几何、工艺设置和聚合物的变化而发生显著变化。
二、影响收缩率的因素
体积收缩率:
是所有收缩率背后的驱动力。体积收缩率如何在厚度方向上以及平行和垂直于单元平面内的流动方向上细分为线性收缩由其他因素决定。塑料的体积收缩率非常高,当塑料从加工温度冷却到室温时,如果未给它施加压力,其体积收缩率通常约为 25%。成型工艺中施加的压力限制了收缩量。PVT (压力/体积/温度)数据显示了压力和温度对收缩率的影响,也即体积上的变化。
高冷却速率:
对于半结晶材料而言,较高的冷却速率会减少材料的晶体成分。由于聚合物冷却快,没有过多时间来形成晶体结构,从而会减小材料的体积收缩率。
填充造成的取向:
长纤维聚合物分子的取向最初由流动过程中的剪切应力引起。当聚合物仍处于高温并且消除了剪切应力时,取向将松弛。当同时存在剪切和冻结时,将会禁止取向。当聚合物有机会松弛取向时,在平行于流动的方向上通常会有较高的收缩率。在某些采用晶体材料的情况下,分子可能会在垂直方向上压缩得较紧,从而导致垂直于流动的方向上收缩率较高,这种情况在倾向于剪切引起的结晶的材料中很常见。如果材料填充了纤维,则纤维的取向要优先于分子取向。纤维的取向不一定在流动方向上。要正确计算纤维取向,必须运行 Autodesk Simulation Moldflow Insight Fiber 分析。不管是什么原因,当平行和垂直于材料取向方向上存在收缩率差异时,就可称之为取向效应。
模具抑制条件:
当零件在模具中时,无法在零件表面的平面内收缩;但可以在收缩在厚度方向上收缩。这会导致在厚度方向上产生较高的收缩率。零件从模具中顶出之后,即可以在所有方向上自由收缩。由于聚合物在处于模具中时无法在零件表面的平面内收缩,这就形成了应力。顶出后,零件会不断冷却,这些应力可能会松弛,从而导致零件变形。冷却速率对模具抑制条件有重要影响。如果模具温度较高,则冷却速率较低,从而会从零件中释放掉更多应力。模具抑制条件与材料也有关。某些蠕变阻力较大的材料会松弛得比较慢,因此往往会有较高的线性收缩。松弛较快的材料往往具有较低的线性收缩。
厚度方向上的温度差异:
如果塑料横截面一侧的模具温度与另一侧不同,则两侧的收缩不会均匀。这会形成一个弯矩,从而导致零件发生翘曲
三、引起翘曲的收缩率变化
当考虑收缩如何引发翘曲时,收缩分为四个变量,如以下部分所述。
冷却不均:
当零件两侧的温度差异足够大时,收缩差异可能会在零件中形成弯矩,如图 1 所示。这种现象称为冷却不均。通过冷却分析得出的温度曲线或温度差异图可以很好地说明这一问题。温度差异越大,发生翘曲的可能性就越大。导致温度不均匀的因素包括:
●冷却管线的放置不佳。
●冷却液温度控制不佳。
●模具热属性。
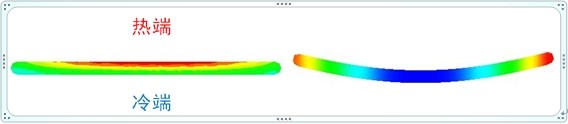
收缩不均:也称为区域收缩或各向同性收缩,这是零件一个区域内或是某个单元内的区域变化。对于中性面和双层面网格,各向同性收缩结果被定义为平行和垂直收缩的平均结果:
SHPar + SHPerp 2
通常,由于在整个零件内存在压力梯度,因此区域收缩率在远离浇口的位置较高,在浇口附近较低。如果在浇口冻结之前已经消除了保压压力,可能不会出现这种情况。区域收缩问题由以下原因引起:
●壁厚变化
●相对于零件较厚和较薄区域的浇口位置。
●工艺设置,尤其是保压时间和保压压力。
冷却系统设计和参数:
图 2 显示了因收缩不均造成圆盘翘曲的两个示例。在图 2A 中,零件中心的收缩率非常高,因为中心的厚度增加并且保压时间较短。这将导致零件形状上的翘曲,这种翘曲通常称为鞍翘曲。在图 2B中,一个较厚的参数导致零件在零件参数上的收缩率较高。这将导致半球体形状的翘曲。
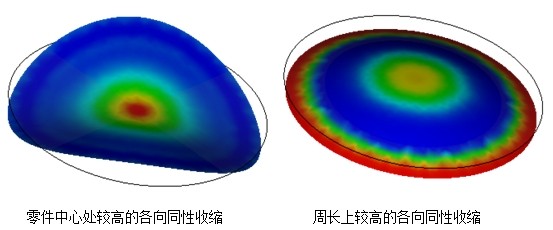
取向效应:是按照流动分析中所确定的分子和/或纤维的取向方向导致的平行和垂直收缩的差异。
有两个组成可以确定分子的取向:分子在冻结时的方向以及分子在冻结时分子上的剪切应力。对于填充了纤维的材料,取向效应还包括纤维的影响。通常对于未填充的材料而言,聚合物在流动方向上会收缩得更多。
对于填充材料而言,通常在垂直于纤维取向的方向上收缩得更多。影响取向效应的因素包括:
●浇口位置以及生成的填充图案和平衡。
●加工条件,尤其是填充时间、保压压力和保压时间。
●冷却系统设计和参数。
与收缩不均造成的翘曲一样,取向效应引起的翘曲形状可能会发生变化。在图 3A 中,鞍翘曲由高平行收缩引起。图 4 显示了取向的方向。由于圆盘位于浇口中心,因此平行收缩是半径。由于半径需要比周长收缩得更多,因此零件将发生鞍翘曲或扭曲。在图 3B 中,半球体翘曲由高垂直收缩引起。这就好比周长比半径收缩得更多。
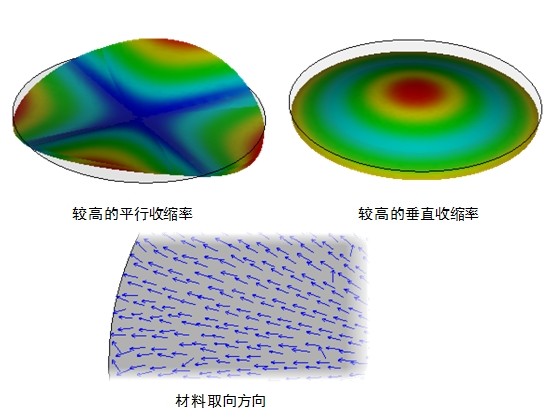
收缩不均和取向效应:
收缩不均(区域收缩)和取向效应之间的差异显示在图 5 中。对于模型中的每个单元,将会计算区域收缩以及平行和垂直收缩。在图 5 中,原始形状是方形的。通过区域收缩,该方形只是越来越小。在计算取向效应时,将会确定平行和垂直于取向方向的收缩率。取向效应的“矩形”面积与收缩不均方形的面积相同。
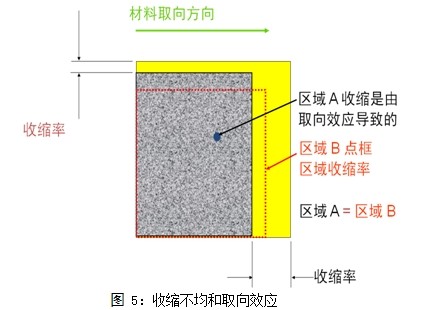
四、收缩预测模型
有两种类型的收缩模型用于中性面和双层面模型,如图 6 所示。一个称为残余应变模型,该模型必须使用测量的收缩数据,被视为是一个经验模型。第二个模型称为残余应力模型。该模型被视为一个理论模型,可以使用收缩数据,也可以不使用。
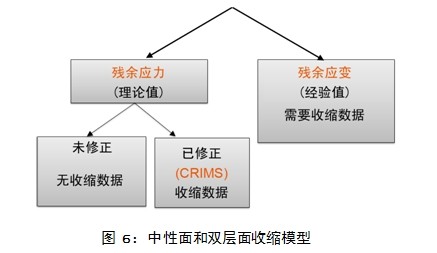
残余应力方法: 残余应力模型将会针对每个单元计算残余应力分布。此分布在与流向平行和垂直的方向上提供每个单元各个厚度上的应力。这种应力分布随后由应力分析程序使用以获取零件的偏移形状。如果材料有可用的实验收缩数据,那么与没有任何收缩数据相比,可以获得相当精确的收缩预测,进而获得零件变形。
残余应力计算的常规说明: 残余应力收缩模型的公式化表达基于热粘弹性材料行为假设条件。它考虑材料在模具中受压冷却时产生的应力。特别地,该模型还考虑热致应力(产生自材料的冻结和随后的收缩)以及压致应力。后一种应力的产生是对形成冻结层的固化材料施加熔压所致。该模型以理论为基础,优势在于即使材料没有可用的收缩数据,模型也可使用。但如果有收缩数据可用,模型性能可大幅度提升。收缩和翘曲的预测均基于计算出的热致及压致应力分布。图 7 显示了当前用于计算过程的一览图。该过程适用于填充了纤维的材料。对于未填充材料,过程大致相同,但无需机械属性计算。
收缩和翘曲的预测均基于计算出的热致及压致应力分布。图 7 显示了当前用于计算过程的一览图。该过程适用于填充了纤维的材料。对于未填充材料,过程大致相同,但无需机械属性计算。
残余应力模型:
下面的方程中显示了常规形式的线性热粘弹性各向异性应力-应变关系。
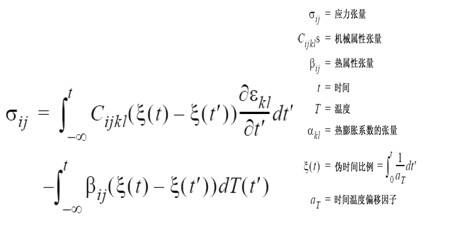
这种热粘弹性模型对不易得到的材料数据极其敏感。当通过实验获得的粘弹性数据不可用时,可使用下面两种形式的粘弹性模型中的一个。
对于无纤维增强材料,模型为各向同性,其中机械特性张量由材料的模量和泊松比定义,存储在 Moldflow 材料数据库中,用于定义热特性张量的热膨胀系数通过材料的 PVT 数据获得。对于纤维填充材料,使用复合材料的各向异性机械和热属性定义这些张量,而属性根据取自流动分析的纤维取向分布计算。这种情况下,模型预测纤维取向方向上的横向和纵向应力。
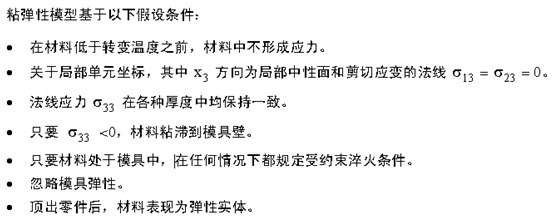
此模型可用于 Moldflow 材料数据库中的所有材料,即该模型可用于无 Moldflow 收缩鉴定的材料。对于填充了纤维的材料,模型要求使用纤维取向流动分析模块。
此模型能够预测收缩趋势,但得到的绝对值可能有很大误差。它对设计翘曲减小方案很有用,但相对于使用收缩数据,此时的绝对值精度较低。对于未填材料,模型具有各向同性,因为流动分析软件中没有计算分子取向效应的功能。
CRIMS 模型
CRIMS 表示 Corrected Residual In-Mold Stress (修正的残余模内应力)。当测量出的收缩数据应用到残余应力模型后,该模型称为修正的收缩模型,即 CRIMS。
未修正的残余应力模型中影响预测精确性的主要因素包括:
●收缩对转变温度和 PVT 数据的敏感依赖性(无法使用现行测量方法表示出实际注塑成型条件下的行为)。
●不能确定分子取向,更无法用于未添加填充物的材料,模型无法预测各向异性。
●缺少针对结晶效应的规定。
●缺少针对粘弹性计算的松弛幅度数据。
如果 Moldflow 鉴定出材料已收缩,则考虑收缩测量结果可大大改进热粘弹性模型。改进方法是将残余应力用作与收缩测量数据相关的混合模型的一个独立变量,以便减小测得的收缩和预测的收缩之间的误差。图 8 显示了一个使用 CRIMS 修正收缩的示例,因此与各种加工条件相比,使用 CRIMS 做出的收缩预测更接近于实际的实验收缩值。收缩修正在平行和垂直方向上完成。
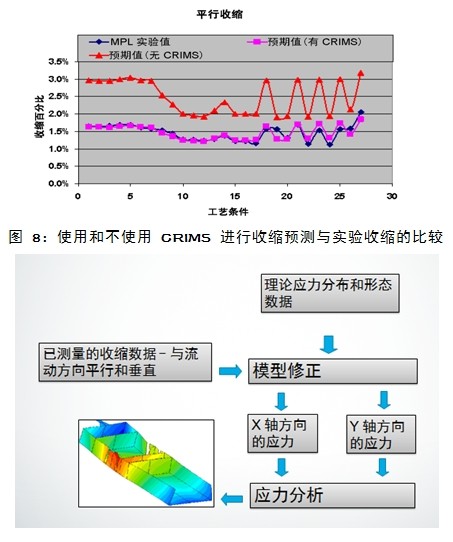
残余应变方法: Moldflow 在其翘曲分析产品中使用的两种收缩预测方法中较早的一种。它基于如下方程。这是一个收缩经验模型。
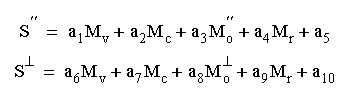
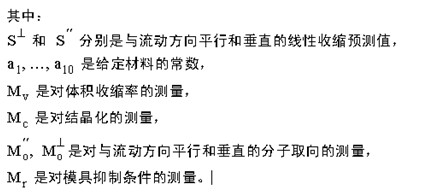
系数 a1……a10是给定材料的常数,由收缩鉴定过程确定,通过构造标准测试件实验获取的收缩数据依据该过程代入以上方程。模型、体积收缩率、结晶化、材料取向以及模具抑制条件的各种测量均通过流动分析模块进行给定翘曲模拟计算得出。以上方程中的收缩模型的适用范围已扩展到包括因模具两侧存在温差而产生的弯矩(通过冷却分析确定)。合并这些效应可给出每个单元上下与流向平行和垂直的收缩。
3D 网格类型的收缩模型:对于注塑成型零件来说,零件被约束在模具中。在注塑成型零件的固化期间,采用两种机制来防止固化层收缩。首先,模具壁的附着力抑制实体层(至少是其外表层)移动,其次,熔压张力使新形成的实体表面保持固定。型腔内残余应力在固化期间形成。因受约束淬火的特性所致,残余应力分布在很大程度上取决于各时期的压力以及冻结层的增长。零件被顶出模具后,这些残余应力以收缩形变形式释放出来。如果初始应变(与型腔内残余应力相等)分布均匀,零件将均匀收缩,不存在任何翘曲或后加工应力。翘曲由整个零件收缩不均造成。
需要考虑两种收缩变化:
区域之间的收缩率变化(收缩不均效应): 对于典型的薄壁零件,这种形式的收缩变化可分为成型件厚度方向上的变化,主要由冷却不均和表面区域到表面区域的变化造成。
不同方向上的收缩率变化(取向效应): 平行收缩与垂直收缩不等以及与纤维取向相关的材料具有各向异性是造成纤维填充热塑性材料零件翘曲的主要原因之一。
注塑成型零件的收缩取决于材料在处理期间的热力行为。为简化理解,我们假设固化零件具有线性弹性行为,熔体具有纯粘性行为。
使用方程近似表示线性收缩是合理的:
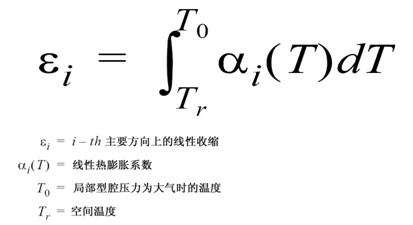
应使用哪种收缩预测模型?
在其上执行收缩测试的每种材料将会经过检查,看看哪种收缩模型最适合。在大多数情况下, CRIMS模型都将是最适合的。如果该模型不是最适合的,将会使用残余应变模型。对于没有收缩数据的材料,将会使用未修正的模型。
最适合的模型将是每种材料的默认模型。建议不要更改这些模型。但是,如果要更改使用的模型,可以从工艺设置向导中“高级选项” > “成型材料”下的流动分析设置中进行更改,如图 11 所示。在“收缩属性”选项卡中,可以更改收缩模型。图 11:选择一个收缩模型。
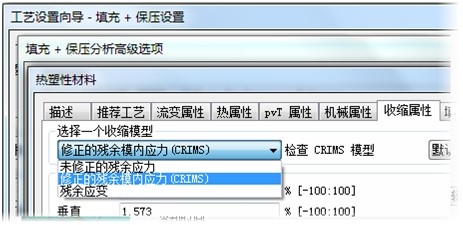