大纲
一:顶针(印)痕的产生说明及探讨
二:顶针(印)痕的产生因数:
1.产品设计
2.模具设计
3.机台及参数选择
4.原料影响
三:顶针(印)痕的产生及解决
一:顶针(印)痕的产生说明及探讨:
1.1 顶针(印)痕:
一般是指在成品外观上所见到的顶白或顶凸,以及在顶针位置正对面可见的不同光泽所显现的暗痕或阴影痕迹(没有顶凸也没有凹陷)。
1.2 顶针(印)痕
是产品上普遍存在的一个缺点,顶针(印)痕的存在极大的影响了产品的外观,鉴于客户的品质要求越来越高,此类问题也需亟待解决。原由的产生是复杂的,涉及到产品设计,模具设计,成型机台及参数,原料影响以及人为因素… …。目前很难完全防止或消除此类问题的发生,很多时候也是在问题发生后才去想办法处理。但是,有些成因还是有依可寻的。 因此,不断积累经验,找出其问题的产生以便及早采取有效预防措施是必要的。
1.3.对顶针(印)痕的产生可以从下面两种试模时的状况去判断:
1).产品在开模后顶针未顶的状况下(有顶针(印)痕)。
2).产品在开模后顶针未顶的状况下(没有顶针(印)痕,但顶针顶出后便产生了顶针(印)痕。
分析以上状况时还可通过产品短射、打脱模剂等方法去多方面寻找原因。
二,顶针(印)痕的产生因数
2.1.产品设计:
产品造型设计的不合理性:
1). 制品肉厚是结构设计时所需要考虑的重要因素 ,增加肉厚既可改善树脂的充模特性又可降低取向应力,减少变形;相反,肉厚过薄会导致塑胶充填困难,继而使成型各项参数随之增加,从而容易产生顶针(印)痕。
2.2模具设计:
1). 浇注系统设计的不合理性:流道太窄,主流道太长,或流道的急剧转折都会使流动阻力
加大 ,从而很大程度限制了塑胶的流动充填,进而影响着成型参数的调整。
2). 浇口设计的不合理性:浇口尺寸的形式,位置,大小,数量。
过小的浇口会造成太大的流动阻力,产生取向应力。浇口附近内应力最大 ,也是应力状况比较严重的区域。
3). 顶出件设计的不合理性:顶出件的类型,排位,大小,位置及数量的影响等,如加强筋、凸缘、塑件斜面等部位。
4). 模具水路系统设计的不合理性:产品在型腔内的冷却不均匀。
5). 模具排气系统设计的不合理性:产品在型腔内处于真空的状态时。
2.3机台参数:
1). 射出参数的不合理性:射出压力以及射出速度的控制及射出切换位置的选择。
2).保压参数的不合理性:保压力以及保压速度的控制及保压切换位置的选择,及背压的大小。
3).模温参数的不合理性:前后模模温参数的差异设定,以及产品对应胶位水路的参数选择。
4).料温参数的不合理性:料管内各段温度的设定。
5).顶出参数的不合理性:顶出速度,压力,方式的设定影响。
6).锁模力参数的不合理性:机台吨位的选择,以及合模力大小的设定。
2.4原料影响
1). 原料选择的不合理性:主要涉及原料的加工参数;其中包括原料的流动性(MI值),玻璃化转工温度等。
三.顶针(印)痕的产生及解决
3.1产品设计:
相对于产品壁厚设计的不合理性,视原料及产品结构而定,一般结构简单的产品肉厚需保证在2.5mm。相对于一些结构复杂,即型腔筋位偏多的产品则需保证其肉厚在 2.8mm。
3.2.模具设计:
1). 为节省原料及后续改模,胶口及流道尺寸设计时一般都不会过大。在产品产生顶针(印)痕的时候可适当加大胶口及流道尺寸,以缓解充填困难而产生的射出压力等参数的偏大(注意:胶口及流道尺寸只有在射出参数偏大时才可修改加大,否则会产生其他一些大的问题,流道末端开排气)。浇口附近的内应力是最大的 ,所以浇口要设在充填容易并且尽量远离顶出件的地方,而且进胶尽量要保证均匀,以便应力位置均匀。
2).顶出件的类型,排位,大小,位置及数量对于顶针(印)痕的产生有着很大关系。设计原则要保证顶针顶出时受力均匀,尺寸适中。如筋位较深部位即产品脱模困难区域等部位需加强顶出,并且顶针需尽量设在筋位上。
顶出过小或离浇口比较近时容易受成型射出压力的影响发生变形 ,模具开模后顶针回弹,从而产生顶针(印)痕。此状况在产品未顶出时便可以看到(如下页图示说明)。
顶针受成型压力变形产生的顶针(印)痕:
先看一个公式:P=F/S
这个是压强公式,P为压强、F为压力、S为力作用的面积
S越大即顶针的直径越大。单支顶针所承受的固定P的能力越强。较大直径的顶针不易被射压挤弯。即不易有射压过后顶针回弹至成品被挤出顶针应力痕。
此类现象的发生也比较常见,在产品未顶出前便可看出顶针(印)痕的存在。对于结构复杂尺寸偏大的产品而顶针尺寸又不够大以及顶针离胶口比较近的情况时较容易发生。此时就需想办法降低成型压力(可通过修改流道,进点尺寸)或修改顶针尺寸来解决。还有一种方式是把顶针改成顶块结构(如斜顶的拆模方式),此目的是为了减少顶针长度从而达到减少顶针受力变形的问题发生。
此方式对于改善顶针(印)痕有很明显的效果,通常在顶针咬花后或顶针高度降过几十条后都未能改善的状况下,可尝试使用此方式处理。
顶针受脱模产品压力产生的顶针(印)痕:
对于一些筋位偏深的产品来讲,需要将顶出的受力点放到那些深的筋位上。以避免顶针在顶出时由于受力过大而产生顶针(印)痕。
顶针位置的设置要考虑是不是在最大着力点上与是否平衡顶出。
顶针与模具钢料的導熱係數不同压力产生的顶针(印)痕:
这种现象在高光面产品会有较大程度的影响,主要是顶针材质与模仁材质不同的导热系数产生,还有顶针与模仁间存在必要的间隙以及润滑油等,导致传热速度不一样,存在温差,而温差又导致塑料在此局部冷却速度不一样,因為溫度差而使产品表面顯現出來不同的亮度,模溫越高越明顯,通常解决方案有以下几种:
1). 将顶针位置加胶 0. 05~0.20mm即可改善此影响,作用是让胶跑到顶针的地方时产生乱流减少塑胶分子链的拉升受力,相应的也就减少了该部位在塑胶冷却后的应力集中现象
2). 另外还有种方式是在顶针表面做咬花或皮纹处理,此方式对于镜面产品的应力痕有一定的改善效果,原理同上。
3). 用铍铜做镶件将顶针(或斜顶)装在铍铜镶件里面,成型时快速传递热量,可以减轻应力痕---此方式使用的很少.
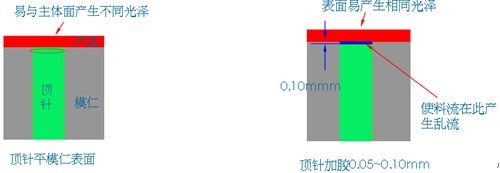
模具水路影响所产生的顶针(印)痕:
1). 一般情况下,模温较低时容易产生应力,适当提高温度温可减低应力的产生,此方法是为了应付产品造型设计不妥时产生的应力痕,对于顶针印力(印)痕的解决不会有太多效果。
2). 有时当注射速度较高时,即使模温低一些,也可减低应力的产生。
3). 调整冷却水路,保证模具各部位温度的一致性即可。
顶针排气所引起的顶针(印)痕:
1). 通常来将,一副好的模具要看它的排气系统设计的如何;模具排气顺畅时塑胶充填也就会很顺畅,相应你的成型参数就容易控制的多。
2).顶针除了顶出产品的功能以外,还要有帮助模具排出型腔内气体的作用。根据产品结构,模具所需采取不同的顶针大小和材料,塑胶流到顶针附近时因排气效果的差异而产生不同的流动效果,从而使产品表面产生顶针痕迹---此状况较少确认,有争议的地方是:当顶针有排气功能时,它的间隙就会出来,相对于前面所说的,顶针与模具温差而产生顶针(印)痕就有些矛盾,个人认为顶针还是需要有排气的功能为好。
3.机台及参数选择:
1).注塑机选用 : 注射机选用不当,也会产生内应力。那种认为大容量注射机注射小模具中的制品会减少内应力的说法不正确。有时会因为压力过高、喷嘴结构不合适造成较大的内应力。
2). 注塑成型工艺条件 :注塑制品由于成型工艺特点不可避免的存在顶针(印)痕,但工艺条件控制得当就会使状况降低到最小程度;影响顶针(印)痕的有模具温度、加工温度、注射速度、注射压力、保压压力、注射时间、保压时间、冷却时间等。其中温度、压力、速度,时间又是塑料成型工艺的主要因素。
3).加工温度
4).注射压力、速度和时间
5).保压压力和保压时间:对于保压来讲,在产品胶量达到90%以上时开始使用此参数再去做调整。
不可通过射出压力等条件把产品完成打饱,或在产品胶量还很少时就开始切换使用保压。此两种方式都是极为不妥的。保压压力,时间以及切换时间需要控制的很好,这对顶针(印)痕的产生有着很多关系。有时降低保压压力和缩短保压时间有利于取向应力的降低 ,这时你会发行顶针(印)痕其实改善了很多。
6).冷却时间 : 冷却时间不足。产品表面温度还未达到其塑胶材料特性的最高顶出温度时顶出产品,此时易产生顶凸或顶穿等顶出缺陷。
|